In mining operations, the efficient transportation of materials is crucial for maintaining productivity and minimizing downtime. A mining slurry pump is designed specifically to handle the challenging task of moving abrasive, high-density slurries that often contain minerals, rocks, and other particulate matter. These pumps are integral to the mining process, ensuring that materials are moved smoothly from extraction points to processing facilities, or from tailings ponds to disposal areas. The performance and reliability of a mining slurry pump are crucial in preventing costly disruptions and ensuring continuous operation.
The material selection for the components of a mining slurry pump, such as impellers, liners, and casings, greatly impacts its performance, longevity, and maintenance costs. Pumps exposed to abrasive slurries tend to wear out more quickly, resulting in increased downtime and higher maintenance costs. Selecting the right materials can prolong pump life, improve performance, and decrease the frequency of repairs. Metal linings, known for their strength and durability, can withstand extreme conditions. In contrast, rubber linings are ideal for reducing wear from abrasive materials, offering a trade-off between strength and wear resistance.
This article aims to guide decision-makers in selecting the appropriate materials for slurry pump components, with a specific focus on the choice between metal and rubber linings. The goal is to help mining professionals and procurement teams understand how material choice can affect the efficiency, maintenance costs, and overall performance of a mining slurry pump.
Understanding Mining Slurry Pumps
A mining slurry pump is designed to transport slurries, mixtures of water and solid particles, commonly found in mining operations. These slurries are often thick, abrasive, and corrosive, which makes pumping them a complex task. Mining slurry pumps are built to handle these challenging materials without sacrificing performance or reliability.
Slurry pumps play a crucial role in transporting materials, including ore slurry, tailings, and waste. Given the abrasive and corrosive nature of these materials, the mining slurry pump must be constructed from materials that can withstand wear and corrosion. The pump’s components must be able to handle the continuous flow of slurry without significant degradation.
When selecting a slurry pump for mining, key considerations include pump efficiency, durability, and cost-effectiveness. High-efficiency pumps help minimize energy consumption while maximizing material throughput, a crucial aspect in large-scale mining operations. Durability, particularly resistance to abrasive wear, is crucial to extending pump life and reducing maintenance downtime. Finally, cost-effectiveness is a significant factor, as the upfront investment in a mining slurry pump should be balanced with long-term operational costs. Choosing the right materials for the pump components can significantly reduce both initial costs and ongoing maintenance expenses.
Key Components of Mining Slurry Pumps
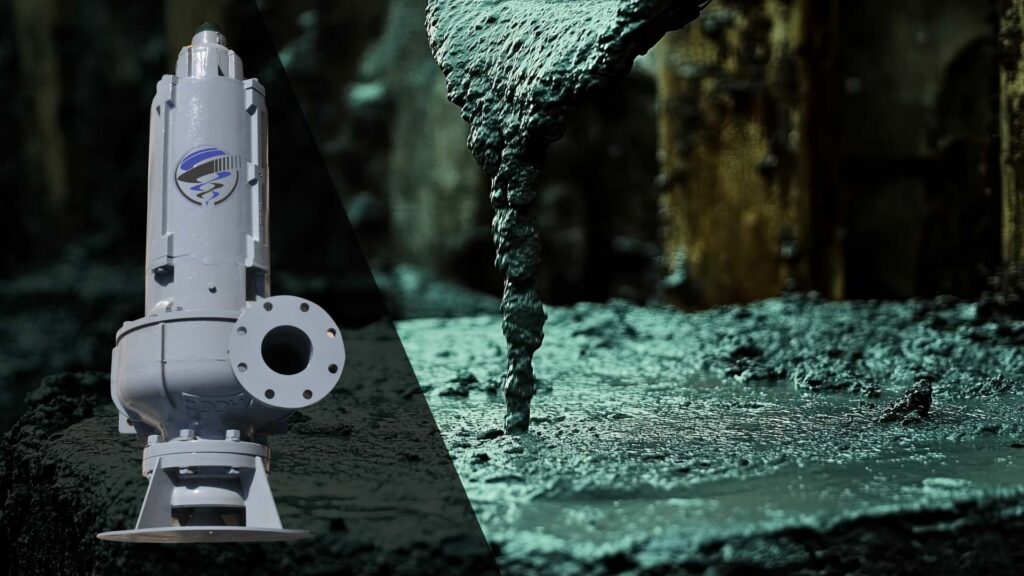
A mining slurry pump is composed of several key components that work together to ensure efficient and reliable operation in handling abrasive and corrosive materials. The most crucial parts of a slurry pump include the impellers, liners, seals, and shafts. Each of these components plays a crucial role in ensuring the pump operates at maximum efficiency while withstanding the harsh conditions typically found in mining operations.
Selecting the right materials for these components is crucial for optimizing pump performance, extending its lifespan, and minimizing downtime. Among these components, the impellers and linings are particularly important, as they directly affect the pump’s wear resistance and its ability to handle specific types of slurries. In this section, we will focus on the materials used for impellers and linings, which are critical decision points for mining professionals and mining slurry pump manufacturers when selecting the best equipment for their operations.
Impeller Materials: Metal vs. Rubber
The impeller is one of the most critical components in a mining slurry pump, responsible for transferring energy from the motor to the slurry, making its material selection a key factor in pump performance and longevity. Impellers can be made from various materials, each offering unique advantages based on the type of slurry being pumped.
High Chrome Alloy Cast Iron (Metal):
Advantages: High chrome alloy cast iron impellers are often the material of choice for pumps handling abrasive, high-concentration slurries. These impellers offer superior wear resistance and excellent corrosion protection, making them ideal for applications where the slurry contains large, hard particles such as gravel, sand, and ore fragments. High chrome alloys can withstand the mechanical stress and wear caused by the continuous movement of these abrasive materials.
Real-world applications: In mining operations, mining slurry pump manufacturers commonly use high-chrome alloy impellers in situations where the slurry is composed of high-hardness materials, such as tailings processing or extraction operations that involve the pumping of coarse ores. These impellers are also highly effective in pumping high-concentration slurries, which contain a large amount of solid matter suspended in water.
Rubber (Natural or Synthetic Elastomers):
Advantages: Rubber impellers, whether made from natural or synthetic elastomers, are known for their excellent corrosion resistance, as well as their ability to absorb noise and reduce vibration. Rubber impellers are ideal for pumping slurries that are less abrasive but contain aggressive chemicals, making them well-suited for mining operations that involve the transportation of chemically treated materials.
Real-world applications: Slurry pumps used in mining applications involving slurries with corrosive chemicals, such as those found in mineral processing, where flotation agents or acids are employed, can greatly benefit from rubber impellers. The flexibility and resilience of rubber also make it suitable for handling fine slurries, where fine particles do not cause excessive wear to the pump components.
Polyurethane:
Benefits: Polyurethane offers a balance of both abrasion and corrosion resistance, making it an excellent choice for mining slurry pump impellers that must handle specific types of slurry. It provides enhanced wear resistance in environments with moderate abrasion, as well as resistance to various chemicals commonly found in mining processes.
Applications and Suitability: Polyurethane impellers are well-suited for slurry environments that require both high abrasion resistance and moderate chemical exposure. These impellers are often used in applications such as coal mining, where slurries can be abrasive but not as chemically aggressive as those found in more complex mineral extraction processes. Polyurethane is particularly effective in slurry pumps for mining operations that deal with moderately abrasive slurries containing light to moderate chemical agents.
By selecting the right materials for impellers and linings, mining slurry pump manufacturers can tailor equipment to meet the unique demands of specific mining environments. Whether dealing with high-abrasion slurries or chemically aggressive materials, choosing the right impeller material will significantly impact pump efficiency, operational cost, and longevity.
Material Selection for Slurry Pump Liners
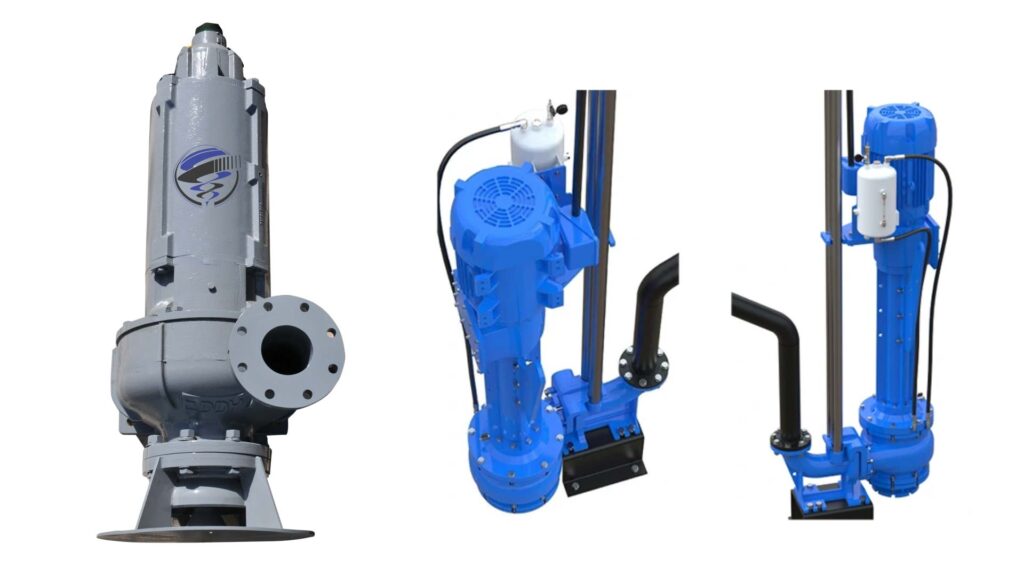
The liner of a mining slurry pump plays a vital role in ensuring the pump can handle abrasive, corrosive, and high-density materials without significant wear and tear. The material chosen for the liners impacts the pump’s performance, longevity, and operational costs. Common liner materials include metal and rubber, each offering unique benefits depending on the nature of the slurry and the specific demands of the mining operation.
Metal Liners:
Benefits:
Metal liners, typically made from high chrome alloy or other hard materials, are designed for durability and resistance to physical wear from abrasive particles. These liners are highly effective in situations where the slurry contains large, hard particles that cause intense wear, such as gravel, sand, and coarse ores. Metal liners provide superior resistance to the mechanical stress generated during continuous operation, making them ideal for high-flow, high-head applications common in mining.
Suitable for high-flow, high-head applications in mining:
In mining, where the material being pumped often includes a high concentration of solid particles, mining slurry pump manufacturers prefer metal liners for their ability to withstand the strain of high-flow, high-head systems. These applications are typically found in dredging, tailings disposal, and other large-scale mining processes where large volumes of abrasive slurries must be handled efficiently.
Rubber Liners:
Benefits:
Rubber liners offer excellent resistance to corrosion, particularly in environments where slurries contain aggressive chemicals or acidic elements. Rubber also provides outstanding wear resistance against fine abrasive particles, reducing the impact of long-term wear and tear. In addition, rubber liners help reduce noise and vibration, making them ideal for environments where minimizing operational disturbances is crucial.
Applications in mining where long-term cost savings are critical:
In many slurry pumps used in mining operations, rubber liners are preferred for handling slurries with high concentrations of corrosive chemicals. These include mining processes that involve the use of flotation chemicals, acidic leaching, or other mineral extraction methods that generate highly corrosive slurries. Rubber liners provide significant long-term cost savings due to their ability to resist chemical damage and reduce the frequency of replacement, making them a popular choice in mining operations where maintaining consistent and reliable performance is essential.
Factors to Consider When Choosing Between Metal and Rubber Linings
Slurry Characteristics
The first consideration when choosing between metal and rubber liners is the characteristics of the slurry being pumped. Mining slurry pump manufacturers assess whether the slurry is primarily abrasive or corrosive in nature. Metal liners excel in handling abrasive slurries containing large solid particles, whereas rubber liners are better suited for corrosive slurries, especially those with acidic or chemical content. Understanding the slurry’s composition is key to selecting the appropriate lining material.
Pump Performance
The material choice for slurry pump liners also impacts pump performance. Factors such as flow rate, head (the height the slurry is lifted), and efficiency must be balanced with the material properties. Metal liners can handle higher flow rates and pressures due to their strength and durability, while rubber liners are better for controlling flow in less abrasive but chemically aggressive environments. Selecting the right material will ensure the mining slurry pump delivers optimal performance over its lifespan.
Cost and ROI
While metal liners typically have a higher initial cost, they may offer a better ROI in applications where durability and performance are critical. On the other hand, rubber liners, with their lower initial cost, can provide long-term cost savings in operations where chemical resistance is more important than abrasion resistance. Mining slurry pump manufacturers often recommend rubber liners in projects focused on reducing maintenance costs and ensuring long-term operational savings.
Longevity and Wear Resistance
Both metal and rubber liners have distinct advantages in terms of wear resistance. Metal liners are highly durable in abrasive environments but may suffer from wear in corrosive conditions. Rubber liners, while less resistant to physical wear from abrasive particles, offer superior resistance to chemical degradation. The lifespan of the liners depends on the specific slurry characteristics and the operational conditions, including flow rate and pressure.
Environmental Factors
Ultimately, environmental factors such as temperature, chemical exposure, and the presence of aggressive contaminants significantly influence the selection of materials. High temperatures and extreme chemical exposure may accelerate wear in both metal and rubber liners, making it essential to select a material that can withstand such harsh conditions. Rubber liners are ideal for environments with constant exposure to chemicals. In contrast, metal liners are better suited for high-temperature applications and those that involve a significant amount of abrasive material.
By carefully considering these factors, mining operators can make informed decisions about the appropriate material for slurry pump liners, ensuring optimal performance and cost-effectiveness over the long term.
Real-World Applications of Metal and Rubber-Lined Pumps in Mining
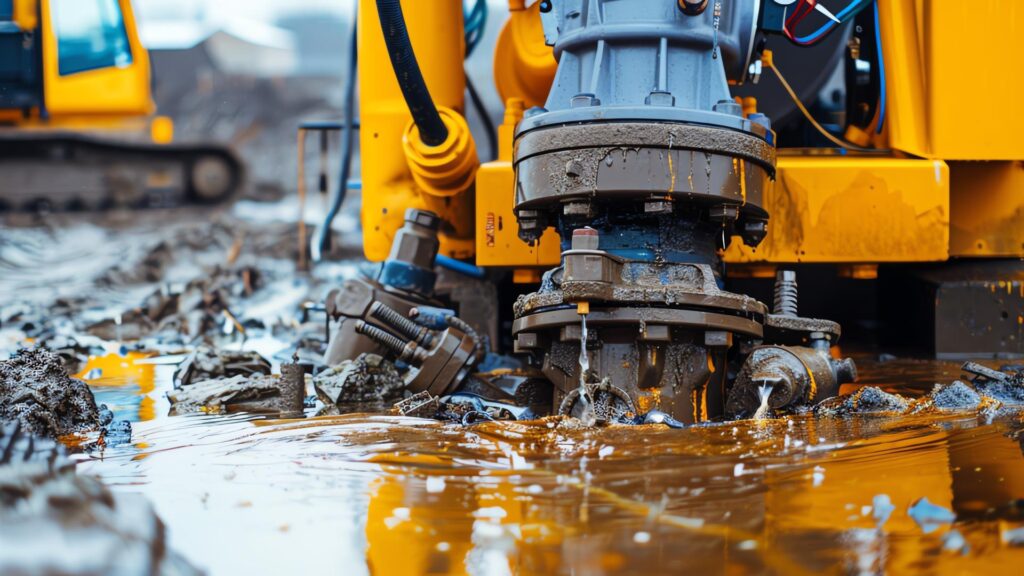
The choice between metal and rubber-lined mining slurry pump components has a direct impact on the pump’s performance and efficiency in mining operations. Case studies from various mining scenarios provide valuable insights into how material selection influences pump functionality and operational costs.
Case Studies Highlighting the Performance of Metal vs. Rubber Slurry Pumps
- High-Abrasion Mining Scenario (Metal Liners): In gold mining operations, where the slurry contains a high concentration of coarse materials, such as sand and rocks, mining slurry pump manufacturers often recommend high-chrome alloy metal liners. These metal-lined pumps are particularly effective in handling abrasive slurries, as they are designed to withstand the mechanical wear caused by the grinding of hard particles. A key example is in large-scale dredging projects, where slurry pumps for mining systems equipped with metal liners effectively manage high-density tailings, eliminating the need for frequent maintenance.
- Chemical and Corrosive Slurry Handling (Rubber Liners): In copper or nickel mining, where slurries are often mixed with corrosive chemicals like acids, rubber-lined pumps provide superior protection against corrosion. Rubber liners protect pump components from degradation in chemically aggressive environments, thereby ensuring longer pump life and reducing the need for costly repairs. In this scenario, rubber-lined slurry pumps for mining systems excel at handling corrosive slurries, delivering consistent performance without the chemical damage that metal pumps would suffer.
Performance Comparisons: How Material Choice Influences Pump Efficiency and Downtime
Material selection has a significant impact on the efficiency and downtime of mining slurry pump systems. Metal-lined pumps, due to their hard-wearing properties, are suited for abrasive slurries where the pump faces constant contact with large particles. These pumps offer higher efficiency in terms of throughput and maintain consistent performance over longer periods, reducing downtime caused by wear. However, they require more frequent maintenance in chemically aggressive environments, as they can corrode over time.
On the other hand, rubber-lined slurry pumps for mining systems, while less resistant to abrasive wear, perform exceptionally well in environments where chemical resistance is more critical. Rubber liners reduce downtime by minimizing the need for repairs due to corrosion, but their efficiency can be compromised in high-abrasion conditions. Therefore, understanding the specific requirements of the mining operation is crucial in determining the optimal material for liners.
Selecting the Right Slurry Pump for Mining Operations
For procurement heads and engineering managers, selecting the right mining slurry pump involves several key considerations that directly affect the performance and operational costs of the mining process.
Key Considerations for Procurement Heads and Engineering Managers
- Flow Rate and Total Head: The required flow rate and total head are critical factors in determining the type of slurry pump and the material for the liners. For applications requiring high-flow, high-head pumping, metal-lined pumps are typically preferred due to their ability to handle the added pressure and flow without compromising performance.
- Slurry Properties (Density, Viscosity, Particle Size): The density, viscosity, and particle size of the slurry will determine whether a rubber or metal-lined pump is the most suitable option. Abrasive slurries with large particles demand a robust metal liner, while finer slurries or those with less abrasive properties may be better suited for rubber-lined pumps.
- Chemical Composition: The chemical composition of the slurry, including factors such as pH levels and the presence of corrosive substances, should be considered when selecting a slurry pump. For highly corrosive environments, rubber-lined pumps are typically preferred as they provide better protection against chemical degradation.
Matching Pump Type and Material to Slurry Characteristics
The key to selecting the right slurry pump for mining is matching the pump type and material to the characteristics of the slurry being pumped. While metal-lined pumps excel in high-abrasion environments, rubber-lined pumps are superior in handling corrosive slurries. Understanding the balance between abrasion and corrosion in your slurry will help you determine whether a metal or rubber-lined pump is the better choice for your operation.
Importance of Consulting Mining Slurry Pump Manufacturers for Expert Guidance on Material Selection
To ensure the correct selection of mining slurry pump components, it is essential to consult with mining slurry pump manufacturers who can provide expert guidance based on the specific demands of your mining operation. These manufacturers have in-depth knowledge of material performance and can help match the appropriate pump type and material to the characteristics of your slurry. Their expertise ensures that you choose the best solution for efficiency, cost-effectiveness, and long-term durability.
Choosing the Best Lining for Your Mining Slurry Pump: Key Takeaways
When selecting materials for a lurry pump for mining applications, the choice between high chrome alloy and rubber linings plays a critical role in pump performance and longevity. High chrome alloy, with its superior abrasion and corrosion resistance, is the ideal choice for high-abrasion slurries containing large particles and coarse materials. This material excels in demanding mining environments where durability and consistent throughput are essential. On the other hand, rubber linings provide excellent protection against chemical corrosion. They are well-suited for mining operations involving slurries with aggressive chemicals or acids, offering a longer lifespan in such environments with reduced wear and tear.
Ultimately, the choice of lining material should align with the specific demands of your mining operation. For high-abrasion, high-flow scenarios, mining slurry pump manufacturers typically recommend high chrome alloy liners. However, for chemically aggressive environments, rubber linings offer the best balance of durability and corrosion resistance. Understanding the slurry’s characteristics, including its abrasiveness and chemical composition, is crucial in selecting the right material for optimal pump performance.For personalized guidance on selecting the right slurry pump material for your specific mining needs, contact Mazowe Dredge. Our experts can provide tailored advice and recommend high-performance slurry pumps and materials suited to your operation.